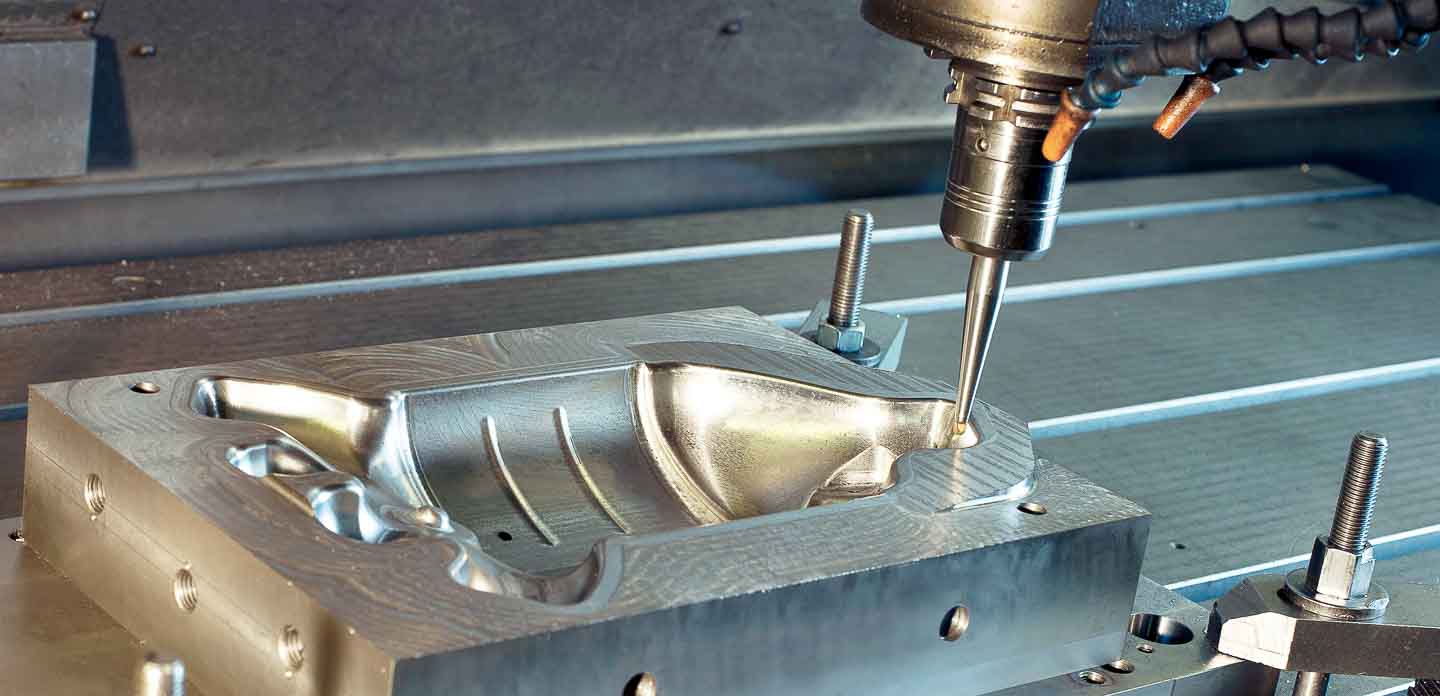
A complete set of injection mold have a variety of parts, each part of the mold pays different role and the steel to use are different as well. Choosing the proper mold steel can ensure high quality mold, efficiency and lowest cost.
How to choose the injection mold steel?
Important steel properties include:
- Ease of machining
- Dimensional stability after heat treatment
- Wear resistance
- Surface finish
- Corrosion resistance
Mold steel we selected frequently are 1.1730, 1.2343, 1.2344, 1.2312, 1.2738, 1.2083, etc. Normally we categorized them as preharden steel or harden steel, preharden steel can be machined and used directly after purchase, harden steel required heat treatment during process, the machining take longer time, injection mold made by harden steel usually have long service life.
Production volume and mold complexity: For a small or finite run on a simple, single-cavity mold, it’s fine for the mold to be made of an inexpensive material like aluminum, which is easily machined and not expected to last for a long time. Conversely, greater production volumes and complex, multi-cavity molds call for the durability of hardened steel.
Cost: Generally speaking, the harder the steel, the more effort and expenditure that will go into it – and the higher the cost. While they cost more upfront, harder steel molds last considerably longer and return higher-quality parts with greater consistency. The same can’t be said for molds built from softer metals, such as P20 steel and aluminum, which can be easily machined for less cost but don’t hold up to long-term repeated use.
Corrosion resistance: Stainless steel is usually the mold material of choice since it resists corrosion, pitting and wear, while also supporting smooth finishes. For maximum corrosion resistance, however, the mold steel should be selected to correspond with the plastic injection molding materials injected into it. Careful attention must be paid to if the plastics have a high degree of acidity, such as resins in the PVC family, or additives like flame retardants.
In the case of halogen free flame retardant DSM thermoplastics, standard steel types can be selected. Beryllium copper inserts may be used for improved cooling near hot spots. High heat conductivity is also required for gate drops in hot runner molds. Standardization of mold parts is growing, not only for ejector pins, leader pins and bushings, but also for mold plates and even complete mold bases. These standard mold bases require only machining of the cores, cavities and cooling channels and fitting of an ejection system. Advantages are:
- Cost savings 30-50%
- Short delivery times
- Interchangeability
- Easy and rapid repair
Making informed decisions about materials for the mold and materials used in complex injection molding projects improves overall plastic part quality and production efficiencies, allowing for reliable products to consistently get to market faster, differentiating you from your competitors.
Welcome to Salda Metal company and contact us. The technicial engineers from Salda Metal will give you the best solution, and recommend the suitable materials for you. We are ready and looking forward to cooperate with your next project. You will be happy and satisfied to be our partner in mould making and injection moluding project.
Industry News
In the January-May period, compared to the same period of 2018, exports amounted to 9.8 million tons with an increase of 20.4% in quantity and 7.2 billion dollars with an increase of 6.5% in value.
Exploring Excellence at BAU 2025 in Munich!
Exploring Excellence at BAU 2025 in Munich! We were delighted to attend BAU 2025, the world’s leading trade fair for architecture, materials, and systems, held in the beautiful city of Munich. This prestigious event brought together industry pioneers, innovative technologies, and inspiring ideas shaping the future of construction and materials. Highlights from our visit: Discovering the latest advancements in building materials and technologies. Connecting with global professionals to share expertise and insights. Strengthening partnerships to foster growth and collaboration. Take a look at some snapshots from this incredible experience! We are inspired by the innovation and ingenuity showcased at BAU 2025 and are excited to integrate these ideas into our work at Salda Metal. Together, we’re building a better future!